Back in high school, my 2nd most ambitious project (the first being
the foundry of course) was to make my own bike pedals from scratch. I had used and broken some pathetic plastic pedals in my time, and decided enough was enough. It was a great project because I got to learn how to use a lot of equipment usually unavailable to the rest of the class including a CNC lathe, mill, and waterjet cutter. This was also when I learned how to do lathe threading, so I could cut those 9/16"-20 LH & RH threads for where the axles thread into the crank.
 |
I had a visionary idea to start a business selling bike pedals that look like ice cream sandwiches. |
One of the problems with the pedals was the fact that I had opted to use plastic bushings instead of ball bearings, and I had no concept at the time of what a tolerance was. The bushing idea came from watching
an episode of Edge Factor about a bike pedal company in Canada that used them. Furthermore, I had never used a CNC lathe before and I actually was the first one in the history of the school to learn how to use it (even before the instructors!). What I ended up producing were axles that were several thousanths larger than the specified tolerance range provided with the bushings which caused them to wear prematurely. I remember spending considerable time at the belt sander grinding them down just so they would fit. If I had known how to use a micrometer, I could've inspected the axles while still in the lathe and readjusted the tool offset so I could hit the correct dimension.
On top of that, I couldn't find the metal supply store that stocked 3/4" chromoly round stock, so I was forced to make the axles out of whatever was lying around.... bad move.
In the case of the pedals that went on my main bike, one of the pedals had an axle made of cold rolled 1018, and the other one was hot rolled. Guess which one broke first? Yes, the hot rolled one, since hot rolled is weaker due to its larger grain structure, making it softer and more flexible. Notice the breaking pattern on the cross section, it's clear that the axle had been cracked part of the way through for a while before it finally broke off. This happened after 5 or so months of use. I had actually machined a new axle to replace the broken one, but over time, I just abandoned the whole project altogether. I knew without the proper steel and heat treatment, this would eventually happen again.
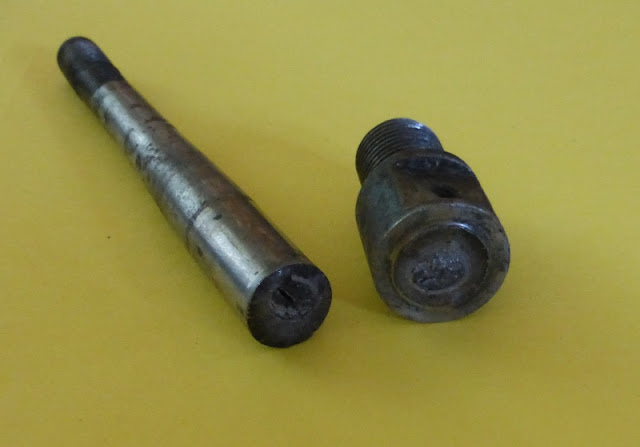
Fast forward a few years later: I bought some more pedals at a garage sale with hopes of rekindling my interest in toe straps. These pedals looked really nice with the leather straps, metal clips, and everything, but for some unknown reason, the designers thought it would be a good idea to hold it all together with a PLASTIC pedal body!!!! Now, you don't have to be The Mike Tyson of Engineering to know that plastic threads strip far easier than metal ones (take the
waffle iron project for instance). I didn't want to waste this perfectly good opportunity throwing out pedals with so many useful parts in tact, so I decided to take the initiative and give pedal building another chance... except this time I would already have a decent axle/ bearing set to work with, so I wouldn't suffer the same fate as before.